The treatment of effluents in steel industries is a complex technical challenge, involving the removal of highly toxic compounds generated during the production of iron and steel.
With processes that use large amounts of water, especially in cooling and gas cleaning systems, steel mills need robust solutions to treat the resulting effluents, ensuring environmental compliance and operational efficiency.
A EP stands out in the development of customized solutions for the treatment of steelmaking effluents. Our approach is supported by one of the largest research laboratories in Brazil, which allows us to carry out detailed treatability studies to identify the most efficient treatment route, meeting the specific requirements of each industrial plant.
Challenges of steelmaking effluents
The effluents generated by blast furnace gas scrubbers can be divided into two main groups according to the reducing agent used:
- Effluents with a lower degree of contaminationAssociated with scrubbers that use coke as a source of carbon and energy.
Effluents with a high contaminant loadResulting from scrubbers using charcoal, with a higher concentration of toxic compounds such as cyanides, phenols and ammonia.
Case studies and technical implementations
- Customer 1 – pilot plant for the treatment of effluent from the blast furnace gas scrubber
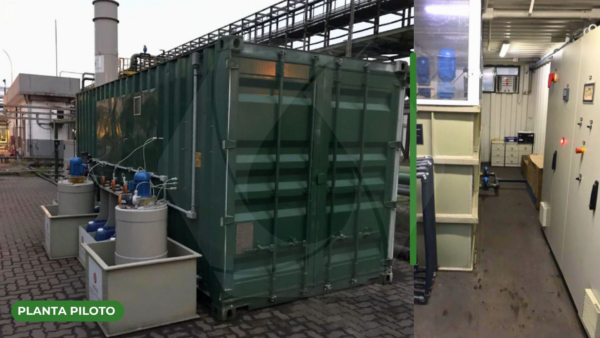
For this client, EP conducted a comprehensive treatability study, which included more than 300 “jar-tests” to analyze the effluent’s response to different treatment processes.
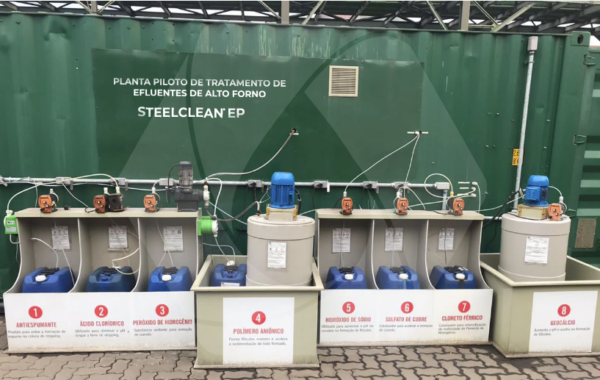
This study was essential for understanding the characteristics of the effluent and designing an industrial plant with a nominal capacity of 120 m³/h.
During six months of continuous operation of the pilot plant, we observed the variations in effluent quality and adjusted the processes to ensure maximum efficiency. The treatment included:
- Neutralization, coagulation and flocculationFor the removal of metals and fluorides.
- Stripping and ammonia absorption: For the removal of ammoniacal nitrogen.
- Oxidation of cyanides and phenolsUsing advanced chemical processes to guarantee the elimination of these toxic compounds.
- Biological purification by MBR (Membrane Bioreactor)For the final purification of the effluent.
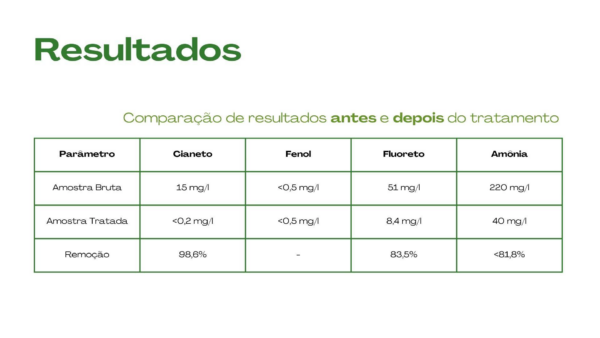
The conclusion of the pilot project resulted in the delivery of the conceptual and basic design for the industrial-scale WWTP, supported by a detailed 3D model.
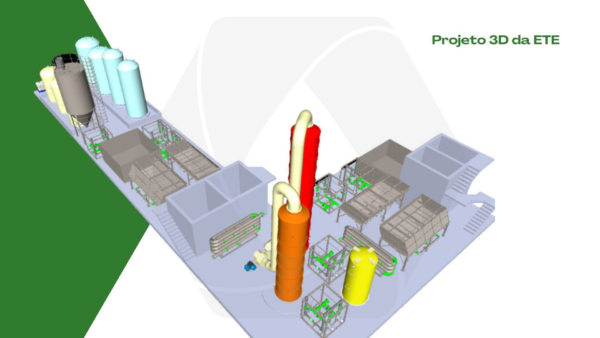
- CSN – Implementation of an industrial-scale wastewater treatment plant
EP was hired by CSN for a turnkey contract, covering everything from the design to the implementation and operation of the WWTP. The project focused on treating effluents with high levels of contamination by metals, ammonia and organic compounds.
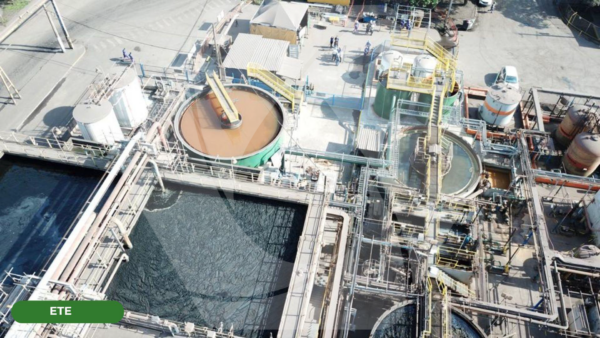
The main stages of the process included:
- Coagulation and flocculation: Removal of heavy metals and fluorides.
- Biological treatmentFor the removal of ammonia and COD.
- Cyanide removal: Carried out by complexation and precipitation with iron and copper salts.
- Physical-chemical polishingTo ensure that the final effluent complies with environmental standards, allowing it to be disposed of safely.
- APERAM – treatability and implementation study
For Aperam, we conducted a treatability study that lasted 8 months, with samples taken at different times of the year to ensure that the solution developed was robust and efficient in all operational scenarios.
The treatment process was structured as follows:
- Coagulation, flocculation and metal precipitationFor the removal of metal contaminants.
- Oxidation with hydrogen peroxide: Focused on the destruction of cyanides and phenols.
- Final polishing with activated carbon: To remove remaining organic compounds.
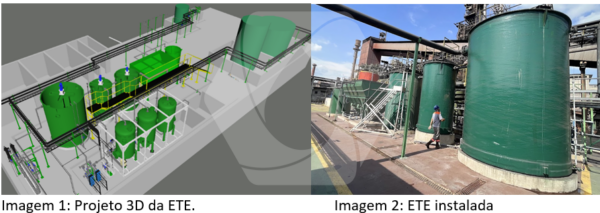
Pilot-scale tests validated the effectiveness of the solution, resulting in the delivery of the conceptual design and detailed stages for implementation on an industrial scale.
- Client 4 – development of the conceptual project for the implementation of a WWTP for the treatment of blast furnace effluents
For this client, EP was responsible for developing the conceptual design of the WWTP, carrying out a trade-off analysis between various treatment technologies.
Our aim was to identify the ideal combination of processes that maximizes contaminant removal efficiency while optimizing operating costs.
The studies were carried out through technical field visits, sample collection and various treatability tests.
The treatment process included:
- pH adjustment and coagulationPreparation of the effluent for flocculation and decantation.
- Automatic decantationUse of decanters with automatic sludge removal.
- Advanced oxidation (Fenton)For the destruction of refractory organic compounds.
- MBR biological treatmentUsing bioreactor membranes for compact and efficient treatment.
The analytical results indicated that the solution developed would effectively meet environmental requirements, providing a treated effluent that is safe for disposal.
EP’s 360° solution: integrated and complete approach
A EP offers an integrated approach through the 360° Solutionallowing industries to centralize all stages of the wastewater treatment process in a single partner.
From the planning and design of treatment plants to environmental analysis, supply of inputs, filter elements, compact systems, chemicals and software tools, EP guarantees a complete and optimized solution.
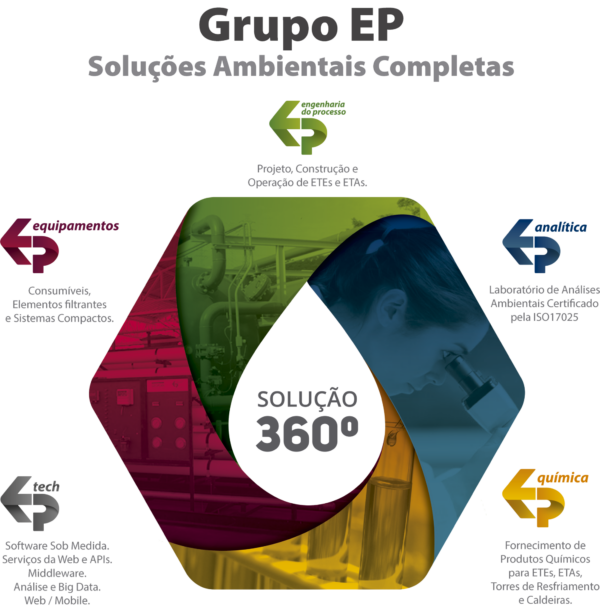
Our operation and maintenance structure ensures the continuous efficiency of the systems implemented, aligning them with the specific needs of each client and in compliance with environmental regulations.
Simplify your operations and achieve excellence with the full integration of our services. If your company is looking for solutions with proven results, we are ready to offer you the expertise you need to boost the sustainability and efficiency of your industrial processes.
Contact us today and transform your effluent treatment process into a model of environmental and operational excellence.